1. 10% Output Increased
This machine has a mechanical structure design for high capacity. Servo controllers are used to elevate capacity for up to 10%. Coordinating with BECKHOFF system from Germany with effective control over co-motion of multiple shafts, redundant waiting time can be mitigated and goals of elevating capacity, stability, and safety can be achieved. Also remote CCTV is available to increase service quality, reduce productive costs, and improve effciency.
2. 20% Preform Weight Reduction
The all-electric linear design going with production of light-weight bottles can reduce 20% of bottle weight. The unique seal design is utilizing theory of pressure to maintain form of cap thread without distortion during blowing. The heating system, focusing on light-weight cap thread, is equipped with an independent cooling system for prevention of distortion caused by overheating of the neck fnish.
3. 30% Energy Saving
There is an air recycling device for re-use of high-pressure air within blow moulding machine for further conversion to be supplied to pneumatic tanks of each unit. Also we programmed the best permutation and combination of heating and reflection boxes which can save 30%~35% of energy waste compared with conventional linear Plastic Bottle making machine.
Product Features
1.The embryo inserting system has multiple safety protection devices to ensure the embryo inserting.
2.Use continuous embryo implantation system.
3.The device for conveying the preform to the heating extension blowing molding adopts a linear structure.
4.All-electric linkage structure ensures high-speed operation and precise positioning of the machine
5.Modular design, easy maintenance.
6.Save cost and increase competitiveness.
7.Improve energy efficiency
8.Human-machine interface control, simple operation
9.Equipped with gas recovery device
10.Low energy consumption, low maintenance, low wear, low poll
Product Configurations
Model |
HZ-CS6-38 |
HZ-CS8-38 |
HZ-CSS9-38 |
HZ-CSS12-38 |
Clamping force(KG) |
60,000 |
72,000 |
60,000 |
72,000 |
Clamping stroke(mm) |
130 |
130 |
130 |
130 |
Stretching stroke(mm) |
320 |
350 |
320 |
240 |
Bottom stroke(mm) |
50 |
50 |
50 |
50 |
Cavity pitch(mm) |
120 |
120 |
80 |
80 |
Number of cavity |
6 |
8 |
9 |
12 |
Max volume(L) |
2 |
2 |
2 |
0.7 |
Neck diameter range (mm) |
30 |
30 |
18-30 |
18-30 |
Max container diameter(mm) |
105 |
105 |
105 |
70 |
Max container height (mm) |
320 |
320 |
320 |
240 |
Carriage unit(pcs) |
120 |
162 |
156 |
192 |
Total power(KW) |
50 |
78 |
49 |
67 |
Air consuming (ltr/min) |
8,000 |
9,100 |
10,500 |
14,000 |
Capacity for 0.5L
(BPH) |
12,000 |
16,000 |
18,000 |
21,600 |
Dimension(mm) |
5,530*1,750*2,600 |
6,600*1,900*2,600 |
6,100*1,800*2,600 |
7,000*2,020*2,600 |
Weight(KG) |
8,000 |
10,000 |
8,000 |
12,000 |
Plastic Bottle Blowing Machine Featured components
Auto-loader
Auto-loader improves working efficiency, accurate transportation, reliable and durable, raw materials are completely free of moisture, pollution, foreign matter, and loss during feeding process. Realize transportation process of feeding process, avoid danger of high-altitude feeding, reduce labor intensity and increase production efficiency.
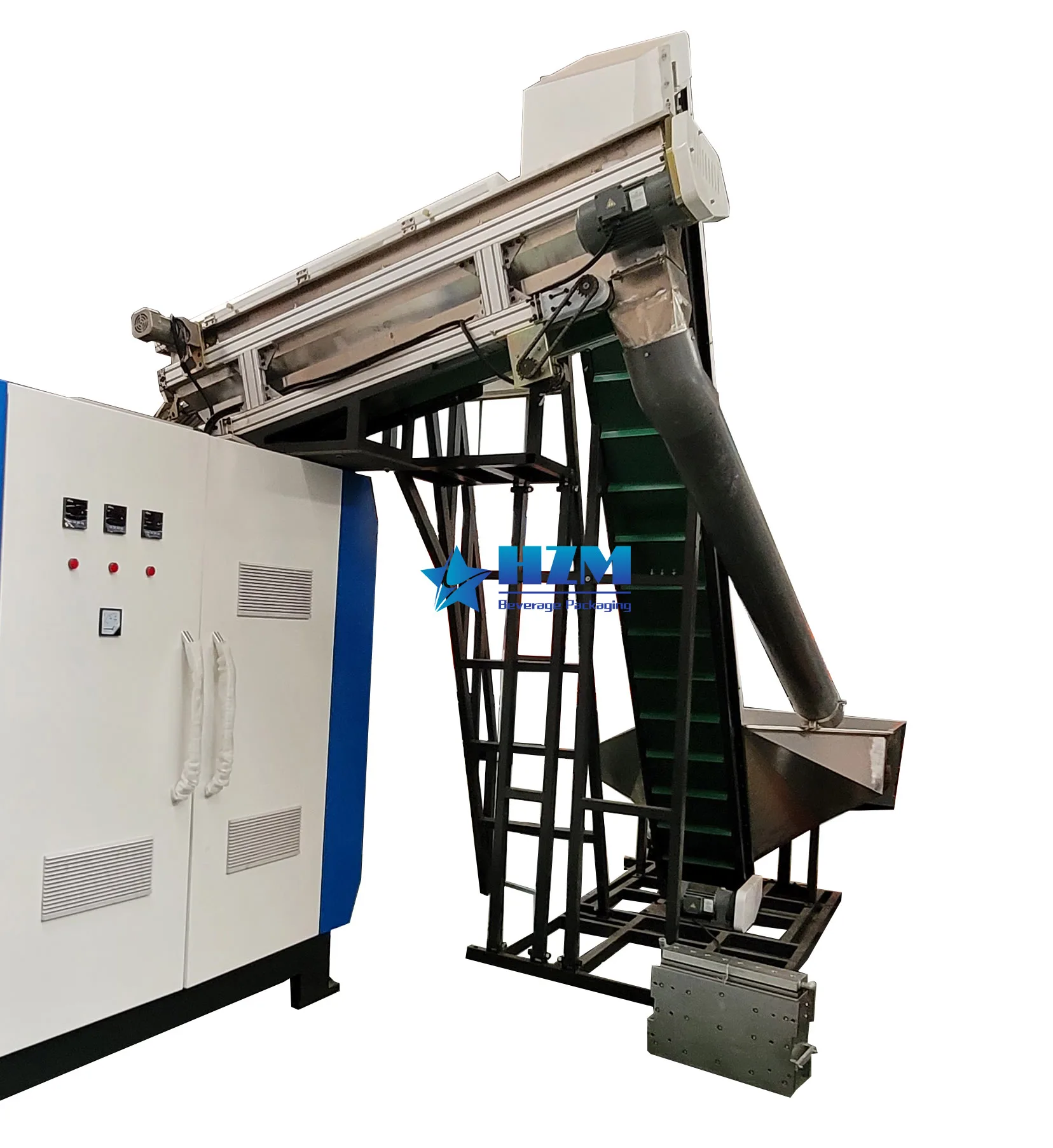
Infrared heating lamp
Adopt infrared lamp heating, strong penetration, preform rotation heating, track revolution, heating evenly, fast and reliable;Heating lamp, reflector width and height can be adjusted to suit preform heating of different structure, with automatic
temperature-removal device to ensure the constant temperature of oven.
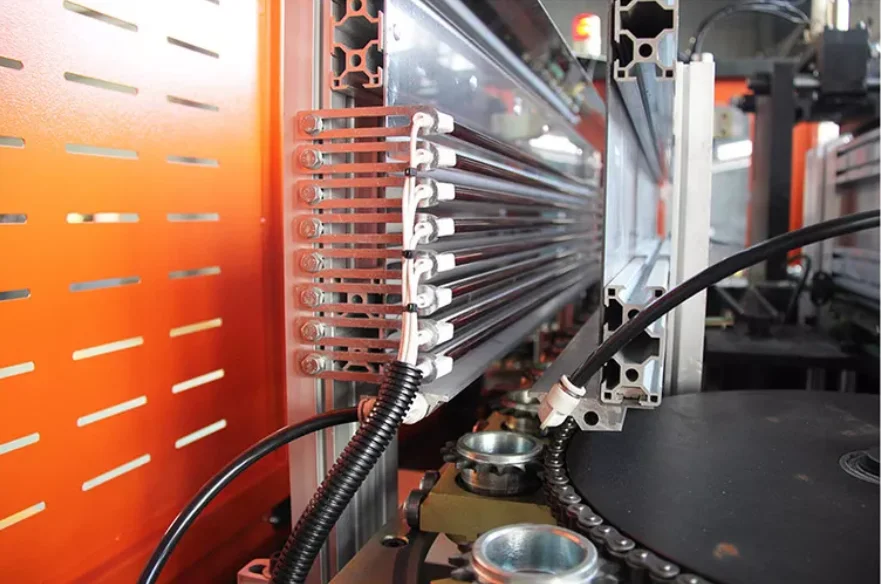
Other attributes
Item |
Remark |
Operation cylinder |
FESTO-Germany |
Pneumatic solenoid valve |
FESTO-Germany |
High pressure solenoid valve |
PARKER-USA |
Programmable controller |
BECKHOFF-Germany |
Digit moldulus output controller |
BECKHOFF-Germany |
Servo motor |
DELTA-Taiwan China |
Retarder |
SIEMENS-Germany |
Photoelectric switch |
BANNER-Germany |
Process
1. Preheating
The preform (embryo) is irradiated with an infrared high-temperature lamp to heat and soften the body part of the preform (embryo). In order to maintain the shape of the bottle mouth, the mouth of the preform (embryo) does not need to be heated, so a certain amount of time is required. cooling device to cool it.
2. Bottle blow molding
This stage is to place the preheated preform (embryo) into the already prepared blow mold, inflate it with high pressure, and blow the preform (embryo) into the required bottle.
The bottle blowing machines on the market are generally divided into two types: fully automatic and semi-automatic.
The fully automatic bottle blowing machine combines the two operations of bottle blowing through the operation of the robot, eliminating the manual process of placing the preheated preform (embryo) into the blow mold. It greatly speeds up the production speed, but of course the price is higher than that of semi-automatic ones.
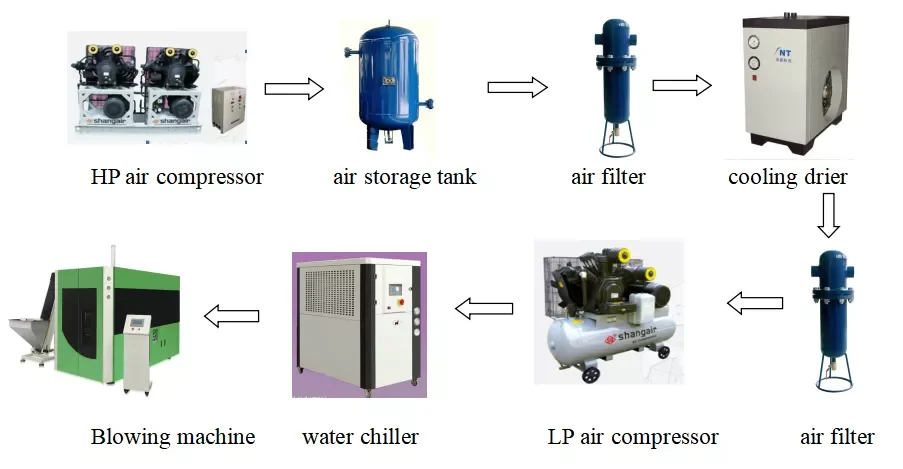