Specifications
Items |
RXGGF16-16-5 |
Amount of working position |
Rinser 16/ Filler 16*2/ Capper 5 |
Production capacity |
5000BPH(0.25L) |
Air pressure |
0.7Mpa |
Air consumption |
1.2 m3/min |
Pressure of rinse water |
0.2~0.25MPa |
Consumption of rinsing water |
1.2T/H |
Filling storage tank volume |
500L |
Main motor power |
3.0KW |
Total power |
5.0KW |
Power source |
380V-3Ph-50Hz |
Dimension |
4500X2230X2700 (L*W*H) |
Weight |
8000KGS |
Configurations
Item |
Brand |
Rinsing pump |
CNP-CHINA |
Back flow pump |
ABB-Germany |
Main motor+ reducer |
ABB-Germany |
Inverter |
MITSUBISHI-JAPAN |
Temperature control |
Omron-JAPAN |
PLC |
MITSUBISHI-JAPAN |
Touch screen |
MITSUBISHI-JAPAN |
Contactor |
Schneider-France |
Sensor |
BANNER-USA |
Pneumatic components |
AIRTAC-TAIWAN |
Sliding bearing |
Igus-Germany |
Advantages:
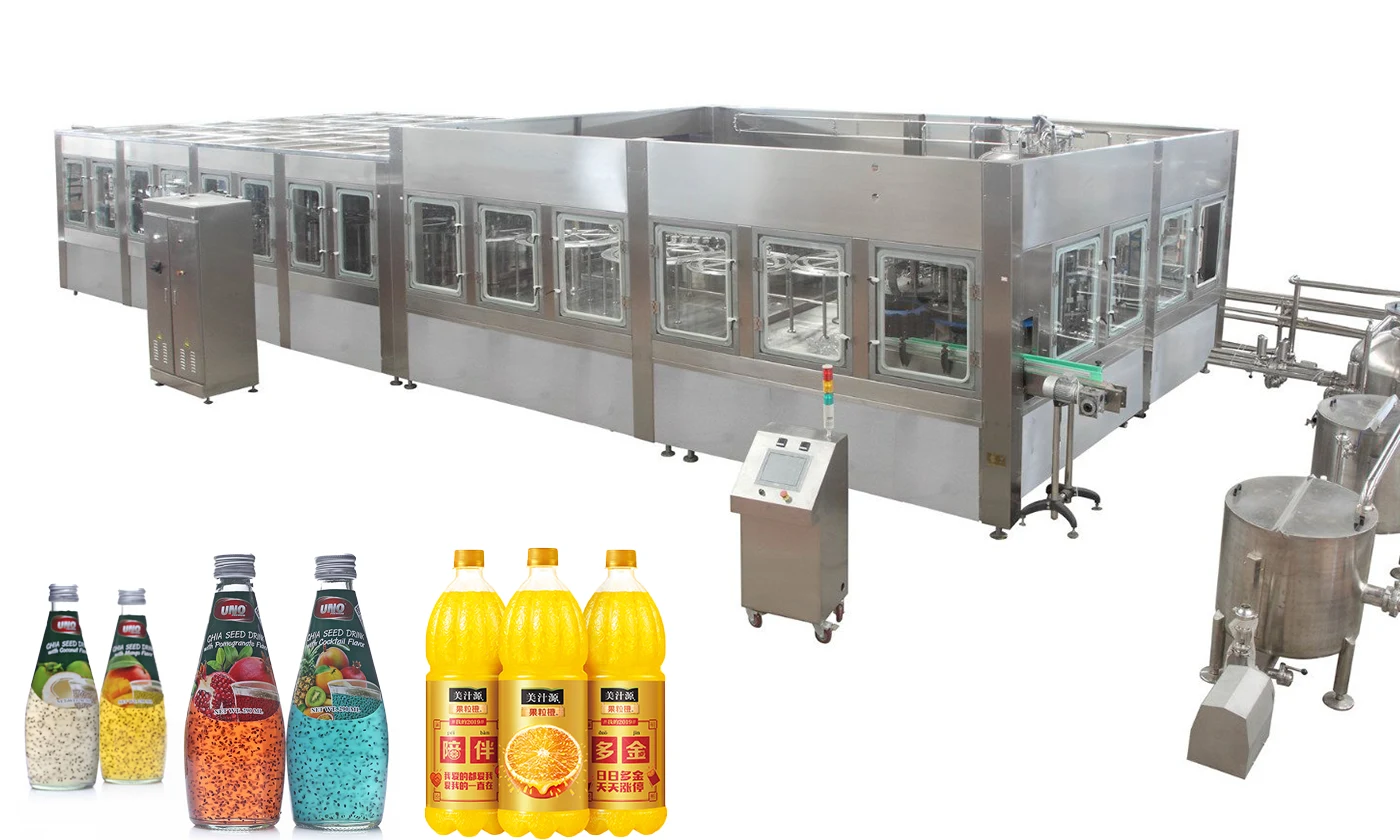
In terms of design, the 4-in-1 juice pulp filling machine fully considers the needs of energy saving and emission reduction, and adopts measures such as high-efficiency energy-saving motors and optimized fluid system design to significantly reduce energy consumption. At the same time, the selection of equipment materials also follows environmental protection principles and can be recycled, reducing waste generation and contributing to the construction of a green and sustainable beverage production system.
In addition, this equipment offers flexible customization services. Customize the 4-in-1 juice pulp filling machine according to your target production capacity and bottle size.
Capacity customization range: 2000BPH-24000BPH.
Bottle customization range: 200ml-2000ml.
Whether it is a glass bottle or a PET bottle, it can be easily adapted and customized to achieve precise filling and packaging.
4 in 1 juice and pulp filling machine is suitable for filling and producing various juice drinks containing pulp, such as coconut juice, pineapple juice, grape juice, apple juice, orange juice, etc. It adopts the advanced micro-negative pressure gravity filling principle, which is fast, stable and accurate in filling. It is equipped with a complete material reflux system, which can also realize independent air return during reflux without contact with the material, reducing secondary pollution and oxidation of the material.
Feature
Rinsing part:
- Except the down framework, the transmission parts and some parts that must be made of SUS304.
- The roller bearing is made of stainless steel, the sealing ring is made of EPDM material, and plastic is made of UMPE.
- The gripper is made of stainless steel, the position where hold the bottleneck is also made of stainless steel, compared with the traditional rubber gripper, it is much hygiene, durable, and no quick-wear parts, the screw parts of the bottleneck can avoid being polluted by the rubber gripper.
- The gripper equipped with high-efficient spray nozzle, it can develop to any position of inside of the bottle, and can save rinsing water. There is a cover above the spray nozzle which can prevent water spilling; and there are regulatory recycle slot and recycle pipes under the nozzles.
- Bearing is made of stainless steel, the sealing ring is made of EPDM material, and plastic is made of UMPE.
- Rinsing time can be guaranteed for 4 seconds.
- By adjusting the height of the rotary parts to adapt for different bottle height
- The motivation is derived from the driven system in the framework passed by gear.
- The supplying of rinsing water is controlled by solenoid valve.
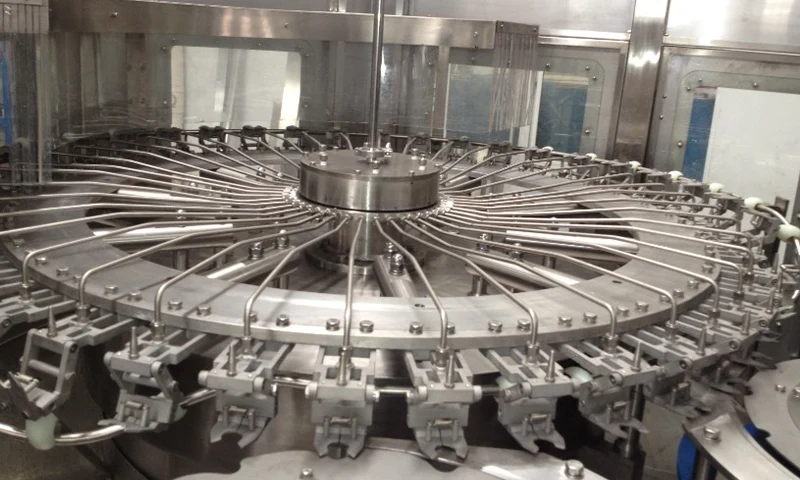
Filling part:
- Adopted Germany igus anti-corrosion non-maintaining bearing that can reduce the pollution of filling to the environment.
- The rotate plate is made of SUS AISI304, large flat toothed bearing.
- The pressure mechanical valve is introduced the advanced foreign design with a fast filling speed, no hygiene corner pocket, a few sealing parts, and precise liquid level control. The whole valve is made of
- The filling system has a CIP circulation system to wash the pipeline and fake-cup used for cleaning filling valve. This system can clean the juice pipe, liquid tank and filling valve etc. effectively.
- This filling system has an automatic temperature control system.
- The filling valve opens and begins filling when it moves down and touches the bottleneck, the filling valve move up and leave the bottleneck when it finishes filling.
- The juice supply adopts the automatic pneumatic valve magnetic liquid-level switch to control the liquid tank automatically.
- Sliding bearing is adopted Germany igus anti-corrosion non-maintaining bearing, that can reduce the pollution of filling to the environment. Rolling bearing made of stainless steel, the sealing ring is made of EPDM material, plastics is made of UMPE.
- The motivation of the filler is derived from the driven system in the framework and passed by gear.
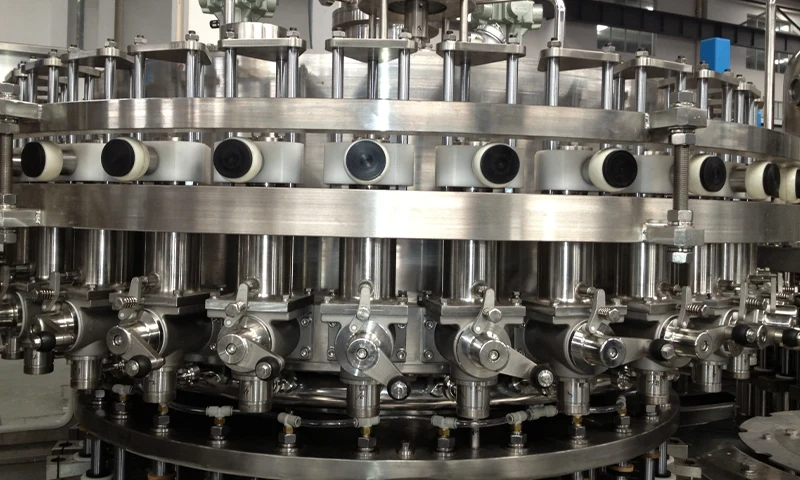
Capping part:
- Introduce most advanced cap sealing technology called France “ZALKIN ". With the help of expert from institute of electro mechanics and mechanical engineering of Shanghai Communications University, we successfully designed. For example: I) the screwing capping head cam (the main parts which can assure the machine run stationary), while adopting “ZALKIN” technology, the expert improve the authenticity and stability of the machine focused on dynamics and kinematics. II) Screwing capping head (the main parts which can assure the capping quality), the expert improve the design of magnetic steel, this improvement can reduce the defective rate of capping better and the traditional character of easy to set and adjust the torque of screwing capping head.
- The screwing capping head is dual-purpose design; it is suitable for flat cap and sport cap.
- The device which can take out the reverse cap and prevent the reverse cap passing is settled in the cap-falling guide.
- A group of photoelectric switches are settled on cap-falling guide. The machine will stop when there is no cap on the guide.
- A bottle inlet detect switch is settled on the screwing capper.
- There are aseptic nozzles between the transition poking wheel and filling parts to rinse the product rested in the bottleneck screw parts.
- There is a cap-lock cylinder in the joint between the cap-falling guide and poking cap plate. It is realize that no feeding no cap.
- By adjusting the height of the rotary parts to adapt for different bottle height.
- The motivation of the screwing capper is derived from the driven system in the framework and passed by gear.
- The main parts of the screwing capper are processed by the digital-control processing center
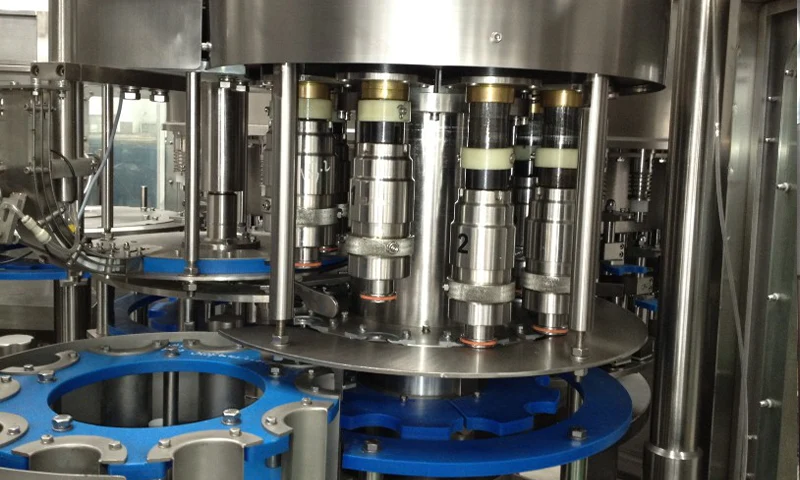