The high-speed fully automatic small bottle filling machine integrates bottle rinsing, filling, and capping functions. It adopts advanced technology, specifically designed for the filling requirements of small bottles. Widely used in industries such as food and beverage, pharmaceuticals, cosmetics, etc.
The fully automatic small bottle purified water filling machine is suitable for the following industries:
1.Food and Beverage Industry: Used for producing purified water, mineral water, juice beverages, etc.
2.Pharmaceutical Industry: Used for producing injection water, oral liquid, etc.
3.Daily Chemical Industry: Used for producing toner, detergents, etc.
4.Chemical Industry: Used for producing chemical raw materials, reagents, etc.
Automatic Small Bottle Pure Water Filling Machine
Tip : You can obtain the price for individual equipment as well as solutions for the entire production line
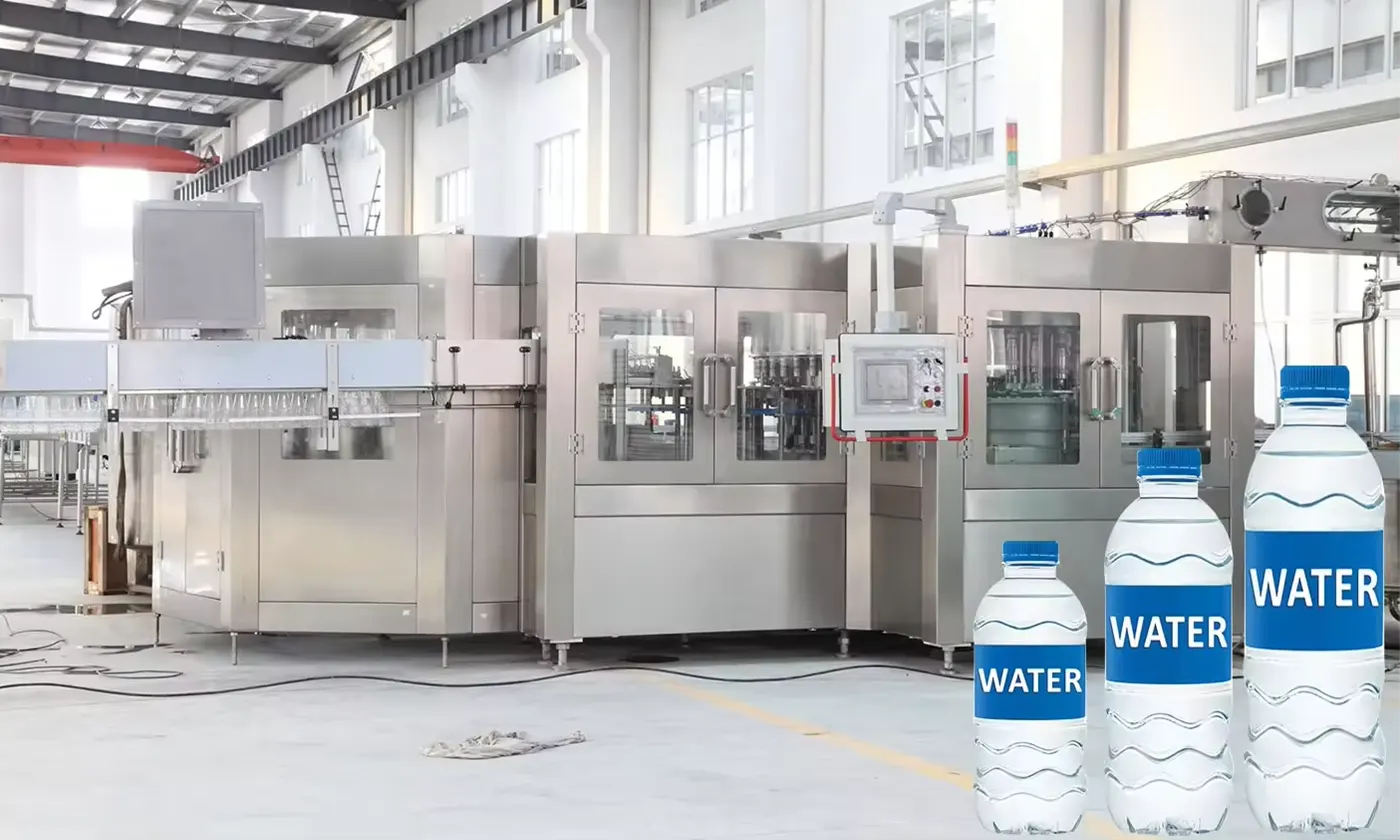

Product Features
1.This water filling machine has a compact structure, perfect control system, easy to operate and highly automated.
2.Only by changing the star-wheel, arch board can realize fill bottle shape change.
3.The parts contact with product is made of quality SUS316/304, anti-corrosive, and easy to clean.
4.Rapid flow, highly filling precision, nicety liquid level without any liquid loss to satisfy the filling process demand.
5.The capping head adopts constant torque magnetic device to guarantee capping quality and impact cap.
6.This water filling machine has a high efficient cap arranging system, perfect cap feeding with self-control and self-protection device.
7.The water filling machine adopts perfect overload protective device can ensure the operator and machine safety.
8.The control system has many functions, such as control producing speed, cap shortage detection, bottle block automatic stop and production counting etc.
9.The main electric and air-drive components are world famous brand products.
10.All control is advanced touch-screen operation and realize people-computer dialogue operation.
Product Configurations
Model
|
XGF14-12-5
|
XGF16-16-5
|
XGF24-24-8
|
XGF32-32-8
|
XGF40-40-10
|
Capacity
|
5,000BPH
|
8,000BPH
|
12,000BPH
|
15,000BPH
|
18,000BPH
|
(for 500ml)
|
|||||
Bottle diameter
|
50~110mm
|
||||
Bottle height
|
160~310mm
|
||||
Air source pressure
|
0.7MPa
|
||||
Voltage
|
380/415V
|
||||
Main motor power
|
2KW
|
2.2KW
|
3.0KW
|
4.0KW
|
7.5KW
|
Dimension
|
2360*1770*2700
|
2760*2060*2700
|
2800*2230*2700
|
3550*2650*2700
|
4360*3300*2700
|
Item
|
Remark
|
Main motor+ Reducer
|
SEW-Germany
|
Inverter
|
SIEMENS-Germany
|
PLC
|
SIEMENS-Germany
|
Touch screen
|
SIEMENS-Germany
|
Contactor
|
SCHNEIDER-France
|
Hot relay
|
SCHNEIDER-France
|
Air switch
|
SCHNEIDER-France
|
Photoelectric switch
|
LEUZE/BANNER-Germany
|
Pneumatic components
|
FESTO-Germany
|
Sliding bearing
|
IGUS-Germany
|
Lubrication system
|
BEKA-Germany
|
Working Process
Bottles are fed from air conveyor into three-in-one rinsing machine via star-wheel. Bottle clamp installed on the rotary wheel of the rinsing machine will grip bottle mouth and make 180º turn along a guide track to face the bottle mouth downward.
In designated section of the rinsing machine rinsing water will jet out from special nozzles to flush bottle inside wall. After
rinsing and dripping, bottles gripped by bottle clamp will make another 180º turn along a guide track to resume bottle mouth facing up.
Cleaned bottles are moved out of the rinsing machine by star-wheel. After entering the fill area, bottles are retained by neck supporting carrier plates which are actuated by bottle carrier mechanism to raise them to engage with filling valves.
Filling is completed by gravity. The material filled into the bottle through filling valve. The bottle goes down and leaves valve to capping machine via neck handling star-wheel.
Anti-rotation blades on capping heads will seize the neck of bottle to prevent it from rotation and hold it in up-right. The
twist-on capping head will make revolving and rotating movement along with the machine to finish the complete capping process of cap picking, placing, twisting and disengaging under the control of a cam.
Rinsing
1.This bottle clamp grips bottle at neck position, avoiding bottle mouth thread contamination caused by rubber gripper block of a traditional bottle clamp.
2.The high efficiency atomizing spray nozzle installed on bottle clamp is capable of cleaning any part of bottle inner wall, saving rinsing water.
3.Covering of bottle clamps and elevator are product of Igus.
Filling
1.Filling valves are designed and manufactured with German technology, featuring high filling accuracy and high filling speed.
2.All sliding bushes of lifting device use Igus (Germany) anti-corrosion maintenance free bearing.
3.Filling valves are made of SUS316.
4.Hydraulic pump is float-ball controlled.
Capping
1.Highly effective acentric way for cap sorting to reduce the abrasion.
2.The fall guide rail has the device to prevent the reversal cap from passing and pick out the reversal cap.
3.It has the bottle check-up switch to control the cap flow and stop it in case no bottle to reduce the cap quantity.
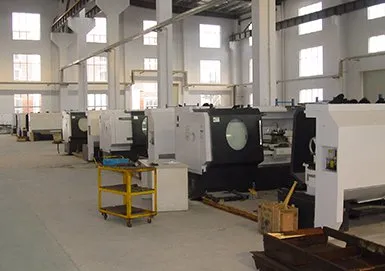
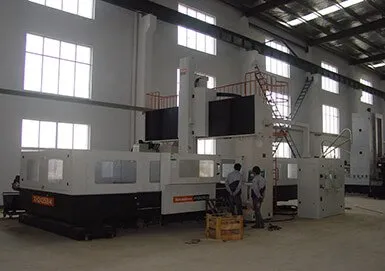
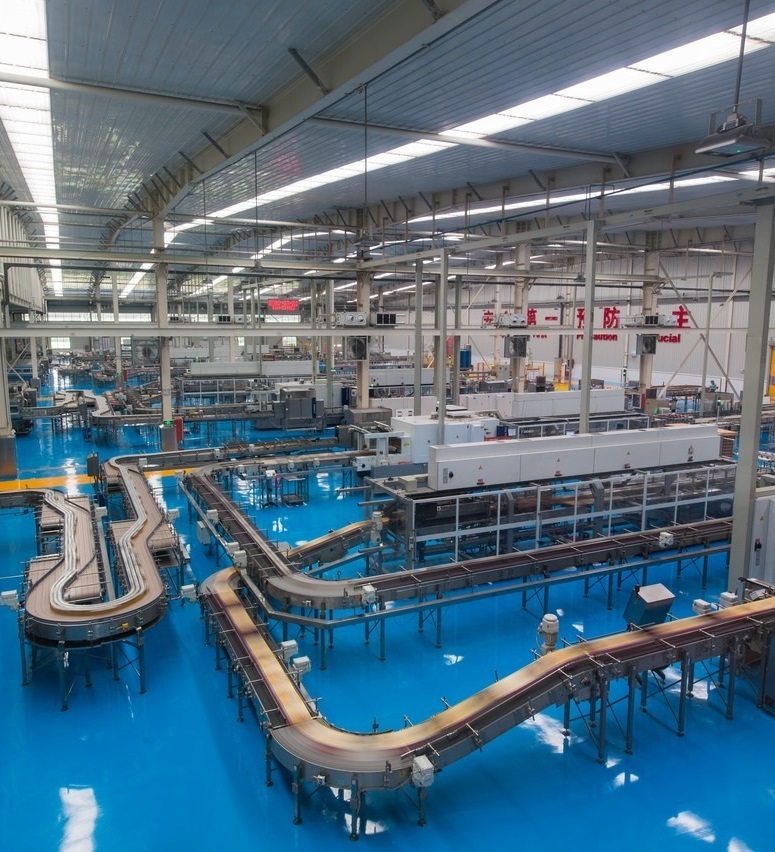
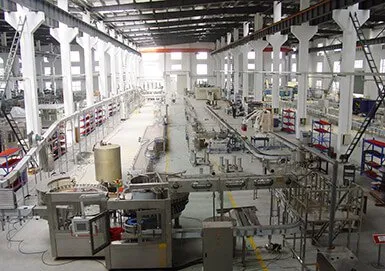
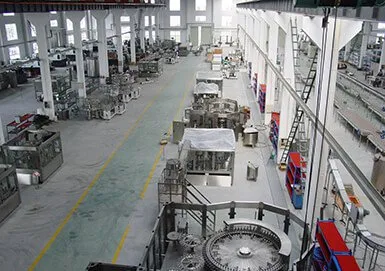